Implementing Process Analytical Technology into Cell and Gene Therapy Manufacturing
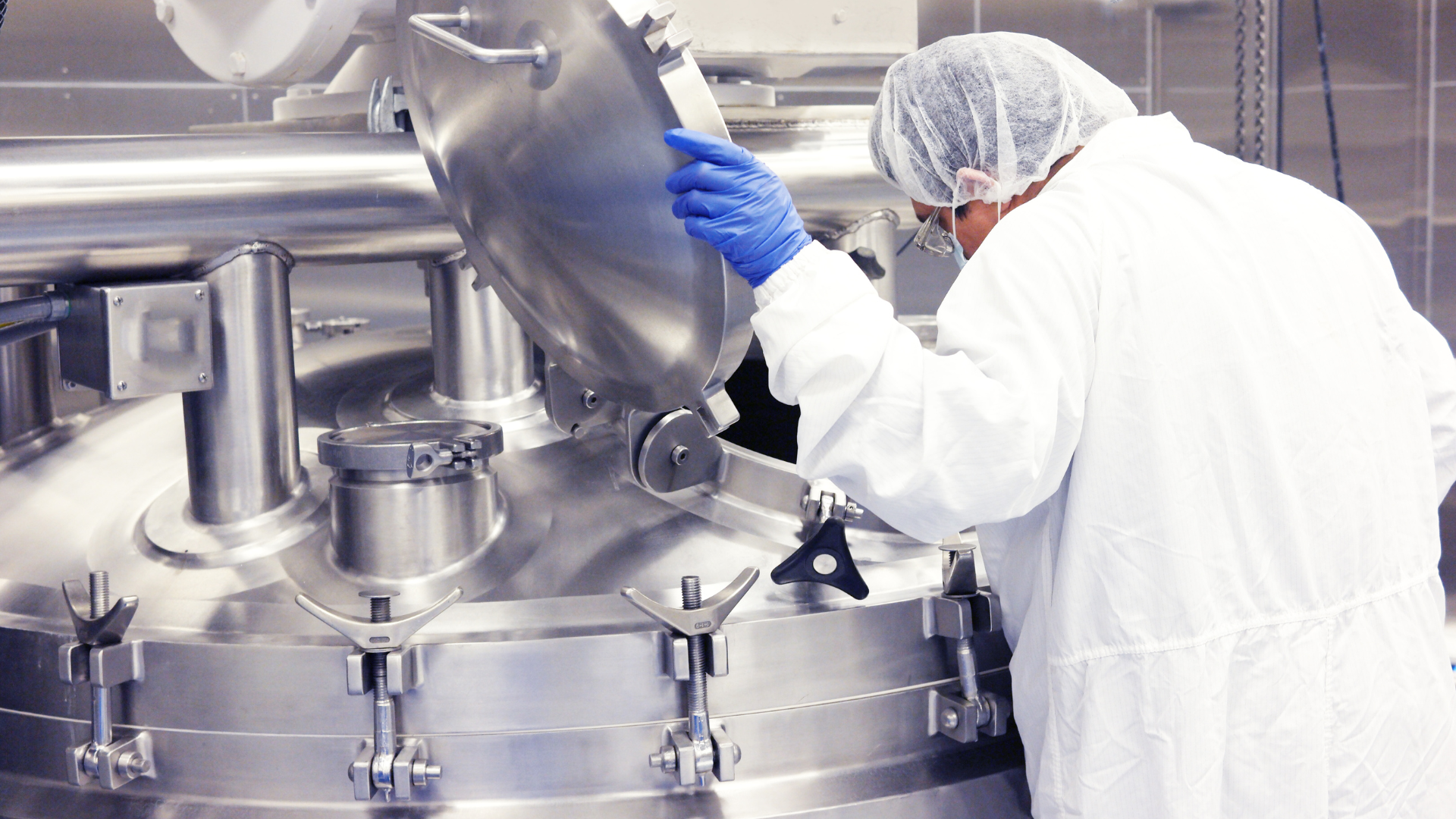
Introduction
Process analytical technology (PAT) allows cell and gene therapy (CGT) developers to better understand and control product manufacture.
According to the US Federal Drug Administration (USFDA), PAT is a methodology used to design, analyse and control manufacturing processes in the pharmaceutical industry. The primary goal of PAT is to measure critical cross parameters (CPPs) that directly affect the essential quality attributes of active pharmaceutical ingredients.
However, researchers claim that the pharmaceutical industry needs more purpose-built monitoring technology. Furthermore, the complexities linked to the manufacturing of advanced CGT products have resulted in the slow adoption of PAT in bioprocessing operations. The unique critical quality attributes and heterogeneity of CGTs present challenges for applying PAT approaches to them.
Case study
A study published in Nature Scientific Reports explored the applicability of a novel refractometry-based PAT system (Ranger system) in monitoring the metabolic activity of HEK293T cell cultures during lentiviral vector (LVV) production processes in real time.
A refractometry-based PAT system relies on a novel advanced refractive index (RI) profiling technology. This technology can identify changes in cell culture composition associated with cellular metabolism.
Additionally, these systems compare cellular activity under variations of bioreactor operating conditions, giving researchers a more in-depth understanding of real-time culture requirements for specific cell lines and products.
Related:
- Improving Control Strategies for Bioprocessing & Cell Culture
- Future Directions for Accelerated Upstream Bioprocessing
- Process Development and Manufacturing Avenues for Gene Therapy Vectors
The Ranger system established that there was a correlation between bioreactor pH and culture metabolic activity. Scientists used this information to create a pH operating strategy that resulted in a 1.8-fold increase in metabolic activity compared to an unoptimized bioprocess in bioreactor experiments.
Yet, the results also indicated that higher metabolic activity was not related to increased LVV production. Instead, the higher metabolic activity was the cells' response to stress the higher metabolic activity was the cells' response to stress. When pH levels are low the cells increase their metabolic activity to maintain optimal cellular conditions. This demonstrates that there is not always a straightforward relationship between critical process parameters (CPPs) and critical quality attributes (CQAs) in such complex systems.
Conclusion
Overall, existing solutions for CGT need to be adapted since the same manufacturing processes used for traditional biologics including sensors for basic process parameters are used for CGTs. CGT manufacturing requirements differ from those in biologics, particularly regarding cell culture conditions.
However, this case study represents a crucial change from a traditional and static manufacturing model to one that is adaptable and based on a comprehensive scientific understanding of bioprocesses. To summarise, this research shows that integrating PAT into biomanufacturing processes would greatly benefit the CGT field by achieving a better understanding of process parameters and product quality attributes.