Gene Therapy Manufacturing
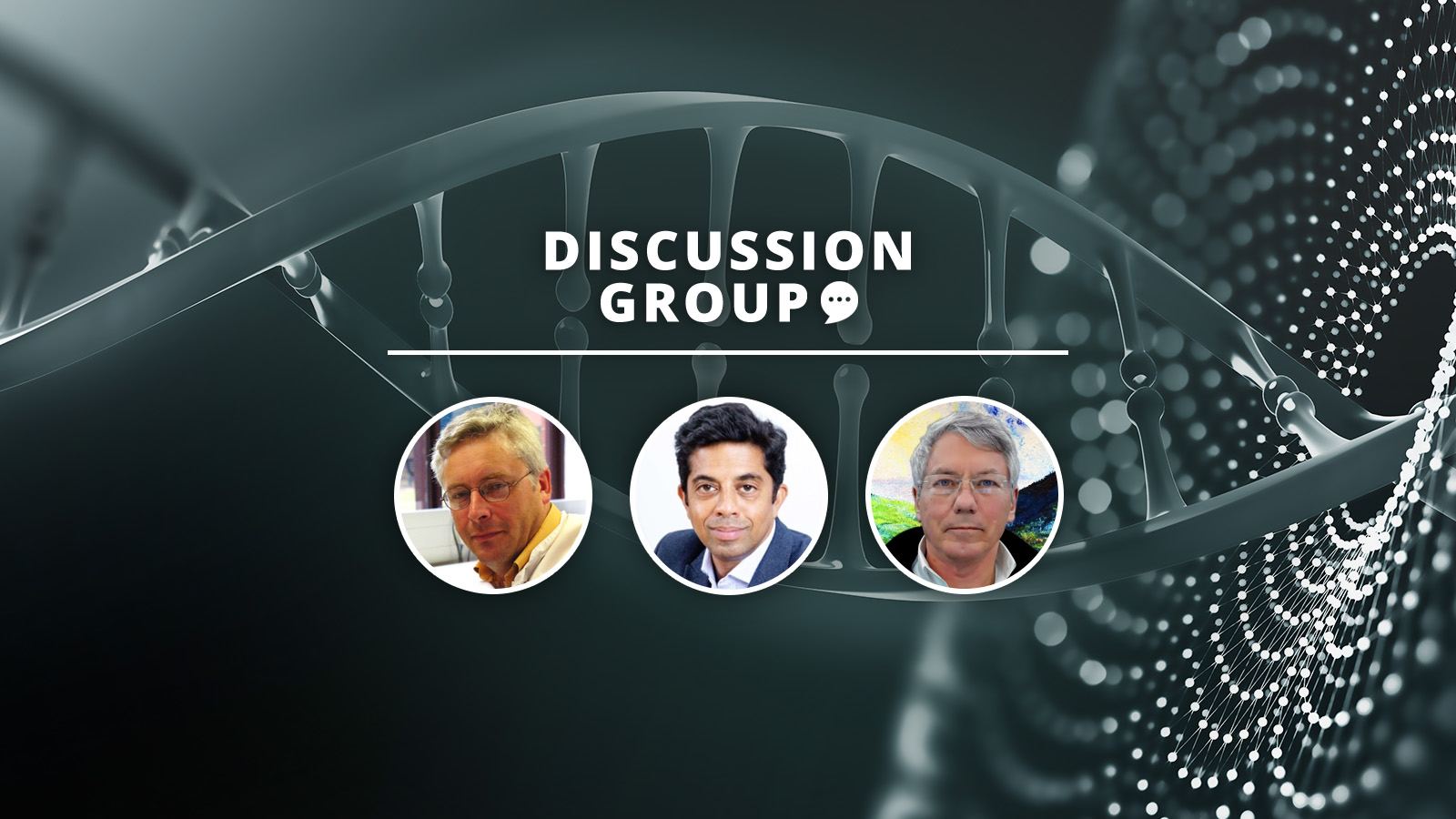
The Discussion Group came together for an hour of specialist discussion about the key hurdles and strategies for manufacturing techniques of cell and gene therapeutics. This Discussion Group was a selection of key industry leaders from various pharmaceutical and biotechnology companies.
Glyn Stacey, Chief Executive at SSCBio, led the discussion. He was joined by Ajan Reginald, Chief Executive Officer at Celixir and Michael Fossel, President and Founder at Telocyte, who were there to support. Key discussion topics included streamlined manufacturing processes, strategies for commercialisation, and expansion to global markets.
Outsourcing Vs. In-House Manufacturing
Reginald began by discussing the decision-making process that goes into gene therapy manufacturing and commercialisation. In particular, Reginald drew from his own experience at Celixir: “when we looked at our novel products back in 2017, we couldn't actually find a contract manufacturer that had experience that aligned with our desired process development.”
To ensure a smooth transition into clinical studies, Celixir decided to take things into its own hands. “Our default position was that there was so much development work to be done, that it was not ready to transfer yet to someone else to manufacture,” Reginald continued. The result - as Reginald explained: “We took the perhaps slightly naïve step to build our own manufacturing facility.”
- Streamlining Stem Cell Manufacturing
- Overcoming the Key Challenges of Gene Therapy Commercialisation
- Inciting Rapid Standardisation in Cell and Gene Therapy Manufacturing
Celixir's undertaking involved developing all process steps and producing a Good Manufacturing Practice (GMP) product to progress into clinical studies. Reflecting upon the decision, Reginald expressed how “although it may have seemed rash at the time, it was necessary due to the lack of transferable expertise available for our novel products”. In-House process development, in this case, provided optimal opportunity to meet key manufacturing components and considerations such as efficiency, economy, and rapidity to facilitate accurate scale-up.
In response, one audience member identified available capital as a further deciding factor when opting for in-house over outsourced manufacturing. An important aspect must be whether “you have the financial ability to build your own facility, whether you have internal process development expertise that you could leverage, and if that synergy can fit with your existing portfolio,” they explained.
“Working with CMOs facilitates an elegant development process into the clinic”
Reginald pointed out that in some cases, as with Celixir, in-house manufacturing can work out cheaper. Conversation then turned to integrated approaches where contract manufacturing organisations (CMOs) can be brought in to help troubleshoot any areas of difficulty. The audience member in question mentioned how in their company, “we haven't quite got our facility up and running yet, so in order to ensure we meet our patient needs we must explore both options in manufacturing.”
CMO Selection: Cost Vs. Risk Balance
Following on from the discussion of in-house manufacturing versus outsourcing, Stacey posed the following questions: “what goes into selecting the right CMO and what decisions need to be made in terms of how you go about progressing with a CMO?” The panel identified the need to use a CMO with a proven track record of delivery who has worked across various companies and platforms.
Reginald also mentioned the “cost versus risk balance” where approaching high-level CMOs entails a higher price tag but a lowered sense of risk. This can provide a streamlined and efficient scale-up process compared to in-house processing. However, the predominant drawback to top-tier outsourcing is a longer time scale. Nevertheless, as Reginald puts it, “working with CMOs facilitates an elegant development process into the clinic, and ensures you are not repeating the same mistakes made by other manufacturers.”
Jurisdiction Considerations
Jurisdiction is another important factor that must be accounted for during gene therapy manufacturing. Fossel pointed out that “manufacturing controls in different countries vary considerably, especially in China.” Reginald agreed, saying, “sometimes you need to have a local partner to conduct local manufacturing procedures that fulfil local regulations.”
Planning for a single trial in a single jurisdiction is simple compared to implementing a global strategy.
Planning for a single trial in a single jurisdiction is simple compared to implementing a global strategy. Consequently, it is imperative to incorporate and build as much optionality into the manufacturing design as possible. Failure to do so results in wasted efforts, material, and an increased timeline which delays the delivery of the product.
Concluding Thoughts
The discussion wrapped up with some final thoughts on the future of gene therapy manufacturing. With conversations happening in the industry regarding the revaluation of traditional approaches to standardisation, innovation seems to be fast approaching the field. At Oxford Global, we couldn't have been more pleased with the turnout for our June Cell Discussion Group. The conversation was engaging, the debate stimulating, and the industry insights invaluable. We will continue our Discussion Group series in September with a session focusing on ‘Novel Technologies Advancing Downstream Bioprocessing'. Learn more about the Oxford Global Discussion Group series at our Cell Content Portal.
Want to find out more about the latest cell therapy news? Register now for Oxford Global‘s Cell UK: In-Person event to advance your understanding of cell-based products to ensure clinical and commercial success.